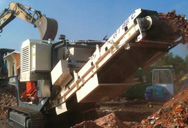
Factors Affecting Ball Mill Grinding Efficiency
The following are factors that have been investigated and applied in conventional ball milling in order to maximize grinding efficiency: a) Mill Geometry and Speed – Bond (1954) observed grinding efficiency to be a function of ball mill diameter, and established empirical relationships for recommended media size and mill speed that take this factor into account.
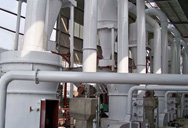
CALCULATION OF BALL MILL GRINDING …
8-3-2013 · calculation of ball mill grinding efficiency. dear experts . please tell me how to calculate the grinding efficiency of a closed ckt & open ckt ball mill. in literatures it is written that the grinding efficiency of ball mill is very less [less than 10%]. please expalin in a n excel sheet to calcualte the same. thanks.
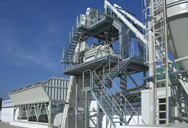
Ball Mill Design/Power Calculation
The basic parameters used in ball mill design (power calculations), rod mill or any tumbling mill sizing are; material to be ground, characteristics, Bond Work Index, bulk density, specific density, desired mill tonnage capacity DTPH, operating % solids or pulp density, feed size as F80 and maximum ‘chunk size’, product size as P80 and maximum and finally the type of circuit …
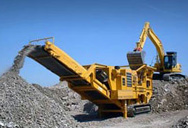
How to Measure Grinding Efficiency
The first two Grinding Efficiency Measurement examples are given to show how to calculate Wio and Wioc for single stage ball mills. Figure 1. The first example is a comparison of two parallel mills from a daily operating report. Mill size 5.03m x 6.1m (16.5′ x 20′ with a ID of 16′). This example shows that Mill 2 is slightly more efficient than Mill 1 even though it has a higher …
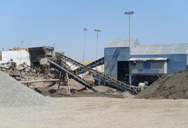
Effect of ball and feed particle size distribution on …
In this article, alternative forms of optimizing the milling efficiency of a laboratory scale ball mill by varying the grinding media size distribution and the feed material particle size distribution were investigated. Silica ore was used as the test material.
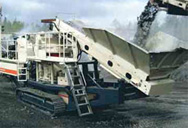
High efficiency ball mill grinding - ResearchGate
High efficiency ball mill grinding Article in Engineering and Mining Journal 209(3):62-+ · April 2008 with 145 Reads How we measure reads
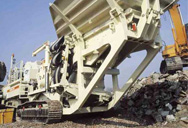
Ball Mills - Mineral Processing & Metallurgy
Working Principle & Operation. The apparent difference in capacities between grinding mills (listed as being the same size) is due to the fact that there is no uniform method of designating the size of a mill, for example: a 5′ x 5′ Ball Mill has a working diameter of 5′ inside the liners and has 20 per cent more capacity than all other ball mills designated as 5′ x 5′ where the ...
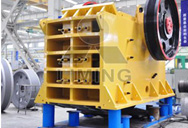
Ball mill - Wikipedia
A ball mill, a type of grinder, is a cylindrical device used in grinding (or mixing) materials like ores, chemicals, ceramic raw materials and paints.Ball mills rotate around a horizontal axis, partially filled with the material to be ground plus the grinding medium. Different materials are used as media, including ceramic balls, flint pebbles and stainless steel balls.
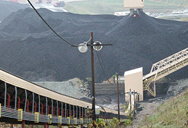
The energy efficiency of ball milling in …
Schellingers calculated ball mill efficiency, in dry or wet ball mill grinding, ranges between 10% and 19%, with the higher figure occurring at the optimal mill loading. In terms of the Brace and Walsh surface free energy of quartz, his results give a ball mill efficiency that is less than 0.5%.
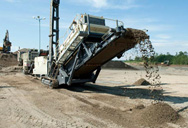
Ball Mills - Mineral Processing & Metallurgy
Metallurgical ContentBall Mill Grinding P80 SizeCylindrical Ball MillsConical Ball MillsRod MillsBall Mill and Rod Mills DrivesGrinding Media & Ball Mill LinersCylindrical VS Conical Ball MillsBall Mill Animation The ore from the crushing section is delivered to the fine ore bin placed at the head of the grinding section, from which it is fed, together with water, to one or more …

Ball Mills - an overview | ScienceDirect Topics
For many decades the two-compartment ball mill in closed circuit with a high-efficiency separator has been the mill of choice. In the last decade vertical mills have taken an increasing share of the cement milling market, not least because the specific power consumption of vertical mills is about 30% less than that of ball mills and for finely ground cement less still.
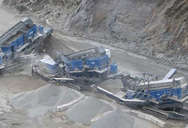
The energy efficiency of ball milling in …
In a second approach, comminution efficiency is based on comparing the energy to produce some size distribution parameter of the product from ball milling with that by single-particle breakage. For both materials, dry ball milling efficiency was found to be in the range of 25%.
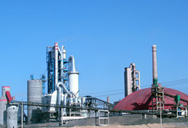
ball mill bayer efficiency - musicforasmile.be
HOME /ball mill bayer efficiency; Stationary Crushers . Grinding Mill . Mobile Crushers . Mining Machine. European Type Jaw Crusher. European Type Jaw Crusher is a new crushing machine, the jaw . LEARN MORE. Jaw Crusher. As a classic primary crusher with stable performances.
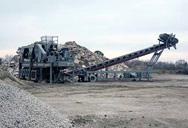
MODULE #5: FUNCTIONAL PERFOMANCE OF BALL MILLING
Ball mill = coarse particles (in the plant ball mill) grinding efficiency Ore grindability (in the lab ball mill) The units of "ball mill grinding efficiency" will be covered in detail in the first part of the module. Alternatively, we can say that: Specific grinding rate = Ball mill x Ore grindability
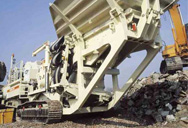
ball mill working principle:improve 20% grinding ...
24-4-2019 · Ball Mill: How to work in Beneficiation/ Dressing Data shows, the cost of ball mill in the mineral ... improve 20% grinding efficiency|Xinhai Xinhai Mining. ...
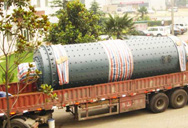
Grinding Efficiency Of Ball Mill - Gesundheitstag …
Grinding Efficiency In Ball Mill Crusher Mills Cone . High grinding efficiency ball mill for cement plant mobile high grinding efficiency ball mill is designed for grinding of clinker gypsum and dry or moist additives to any type of cement the ball mill may operate in either . Read the rest >
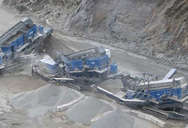
Energy efficiency - IsaMill™ Advantages | Isamill
The large scale of the IsaMill™ makes that efficiency available to mainstream grinding. The high energy efficiency of stirred mills compared to ball mills is well understood. The use of tower mills as an energy efficient alternative to secondary and regrind ball milling became a common inclusion in the latter part of the previous century.
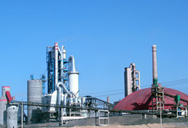
efficiency ball mill, efficiency ball mill Suppliers …
high efficiency laboratory ball mill price brief introduction Raw Material Ball Mill also named as ball mill, raw material mill, material grinding mill and clinker mill, is the key equipment for grinding after the crush process, which is widely used in the manufacture industries, such as cement, silicate, new building material, refractory material, fertilizer, ferrous metal, nonferrous …
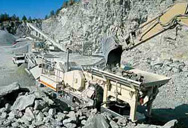
Addition of pebbles to a ball-mill to improve …
B.K. LovedayImprovements in the grinding efficiency of a secondary ball-mill, by the addition of small pebbles from the primary circuit. Proceedings of the XXV International Mineral Processing Congress (IMPC 2010), Brisbane, 6–10 September 2010 (2010) Google Scholar.
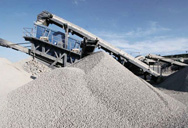
Ball Milling for organic synthesis: A tool for process ...
Ball mills are devices developed for particle refinement + desagglomeration. continuous generation of fresh surfaces with high defect concentration Ball mills are scalable from mL- to m3-scale for lab and industry applications. High mixing efficiency helps to overcome mass-transport-limitations. Direct energy entry by friction and impact