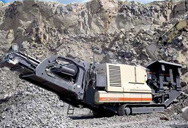
Grinding Method Using A In Cement Ball Mill
Grinding Method Using A In Cement Ball Mill. 2012-8-20traditionally, plants used ball mill to grind clinker and gypsum into cementhe result the majority 60 of finish grinding in the world is still performed using the ubiquitous ball mill ball mills are cylindrical steel shells with steel liners.
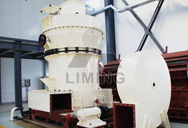
grinding method using a in cement ball mill
Method of Ball Mill by Discrete Element Method collected. The diameter of the gibbsite powder was measured using a Master Sizer 2000 (Sysmex Corporation). Details of the experimental conditions are given in Table 2. Results and Discussion 1. Effects of Fins on Ball Motion in the Mill To predict ball mill grinding behavior using the dis. Get Price

Grinding method using a in cement ball mill - …
Grinding method using a in cement ball mill. Home / Grinding method using a in cement ball mill ; Grinding method using a in cement ball mill; Get Price List Related details. 1. Photo of a 10 Ft diameter by 32 Ft long ball mill in a Cement Plant Photo of a series of ball mills in a Copper Plant, grinding the ore for flotation Image of cut away ball mill, showing material flow through typical ...
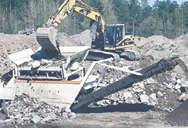
grinding method using a in cement ball mill
Artificial Neural Network Modeling of Ball Mill Grinding Process ... Artificial Neural Network Modeling of Ball Mill Grinding Process, Veerendra Singh, ... the particle size distribution of ball mill product using grinding data available for ... the performance of grinding circuit in mineral, metal and cement industry.
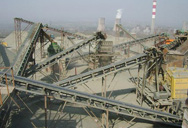
Optimization of Cement Grinding Operation in …
Optimization of Cement Grinding Operation in Ball Mills. Contact Us » Several energy efficient options for cement grinding are available today such as vertical roller mills, roller presses (typically in combination with a ball mill), and clinker pre-grinders with ball mills. Ball mills have been the traditional method of comminution in the mineral processing industries and continue to operate ...
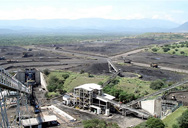
grinding method using a in cement ball mill
grinding ball selection method for cement ball mill 2. The grinding ball is widely used at all over the world for high carbon high alloy casting grinding ball and high carbon low alloy forging grinding ball (or cast grinding balls), in the dry production technology of thermal power plant, cement industry, the vast majority of the use of high, low chromium cast iron grinding ball.
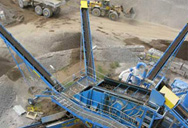
Cement Grinding - Mineral Processing & Metallurgy
Grate Discharge Ball Mills are the rule rather than the exception. Rod Mills for raw and finish grinding begin to enter the picture. Larger and larger diameter mills become common. Lengths tend to shorten. Cement grinding using Grate Discharge principles developed in the ore milling industry applied to the cement industry. This experience plus ...
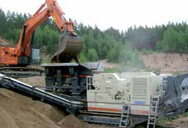
grinding method using a in cement ball mill - …
grinding method using a in cement ball mill Working principle of Ball Mill /ball cement milling. Diese Seite übersetzenKlicken, um auf Bing anzusehen
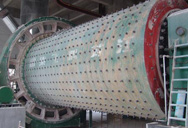
Working principle of Ball Mill /ball cement milling ...
03.03.2015 · Ball mill is an efficient tool for grinding many materials into fine powder. The Ball Mill is used to grind many kinds of mine and other materials, or to select the mine. It is widely used in ...

VRM vs Ball Mill for Cement Grinding - Page 1 of 1
10.02.2016 · VRM vs Ball Mill for Cement Grinding. Good Days! Gentlemen, Anybody in this forum who have had some practical/extensive experience on Vertical Roller Mill being used for cement grinding? We are planning to put up a new cement grinding plant using Vertical Roller Mill(300-350 – TPH) and before implementing the project, we would like to gather as much information regarding the actual …
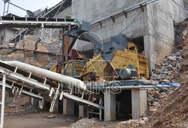
Cement Ball Mill
Cement ball mill is not only suitable for over-flow grinding, but also applicable for cyclic close-flow grinding together with powder collector. There are two ways of grinding: the dry way and the wet way. Features 1. Can work with grinding and drying equipment simultaneously. 2. Easy to adjust the fineness of grinding products. 3. Both dry type and wet type producing.
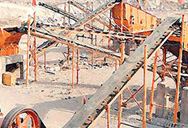
Ball Mill Design/Power Calculation
The basic parameters used in ball mill design ... Rod and ball mill grindability test results should only be applied to their respective methods of grinding. If P is less than 80% passing 70 microns, power consumption will be. Ball Mill Power Calculation Example #1. A wet grinding ball mill in closed circuit is to be fed 100 TPH of a material with a work index of 15 and a size distribution of ...
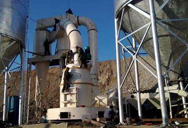
Cement mill - Wikipedia
The grinding action employs much greater stress on the material than in a ball mill, and is therefore more efficient. Energy consumption is typically half that of a ball mill. However, the narrowness of the particle size distribution of the cement is problematic, and the process has yet …
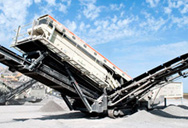
Ball mill - Wikipedia
A ball mill is a type of grinder used to grind, blend and sometimes for mixing of materials for use in mineral dressing processes, paints, pyrotechnics, ceramics and selective laser sintering. It works on the principle of impact and attrition: size reduction is done by impact as the balls …

Grinding trends in the cement industry - Cement …
01.04.2010 · Summary: The main trends concerning grinding processes in the cement industry are still higher efficiency, reduction of the power consumption and system simplicity. In the case of new orders, vertical mills have increased their share to over 60 % and ball mills have fallen to less than 30 %. It is somewhat surprising that the number of different grinding processes and mill types used by the ...

Calculate and Select Ball Mill Ball Size for …
In Grinding, selecting (calculate) the correct or optimum ball size that allows for the best and optimum/ideal or target grind size to be achieved by your ball mill is an important thing for a Mineral Processing Engineer AKA Metallurgist to do. Often, the ball used in ball mills is oversize “just in case”. Well, this safety factor can cost you much in recovery and/or mill liner wear and ...

5 Ways To Improve Grinding Efficiency Of Ball …
According to Bond (1954), the grinding efficiency of a mill depends on the ball mill diameter, size of the media and mill speed. Ball mills with different length to diameter ratios for a particular power rating will produce different material retention times. The longer units are used for high retention ratios while shorter units are used where overgrinding is a factor to be considered.
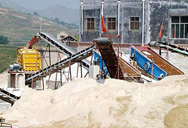
Ball Mill Critical Speed & Working Principle - …
19.06.2015 · If 75 percent of critical speed is considered desirable for efficient grinding in a 2.4 meter (8 foot) diameter mill, then the same will be true for a 5.0 meter (15½ foot) diameter mill. At least ...
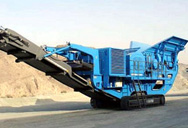
Grinding in Ball Mills: Modeling and Process Control
Keywords: Ball mills, grinding circuit, process control. I. Introduction Grinding in ball mills is an important technological process applied to reduce the size of particles which may have different nature and a wide diversity of physical, mechanical and stone characteristics. Typical examples are the various ores, minerals, limestone, etc. The applications of ball mills are ubiquitous in ...