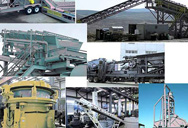
Energy Use of Fine Grinding in Mineral Processing ...
Dec 18, 2013 · Grinding activities in general (including coarse, intermediate, and fine grinding) account for 0.5 pct of U.S. primary energy use, 3.8 pct of total U.S. electricity consumption, and 40 pct of total U.S. mining industry energy …
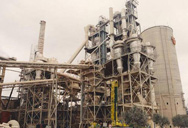
Energy and temperature analysis in grinding
Specific energy is a measure of process efficiency. It relates to the difficulty of machining a workpiece material. It also relates to wheel wear. For example, where the grinding power is 25 watts per cubic millimetre of material removed per second for a particular workpiece material, the specific energy is 25 J/mm3.
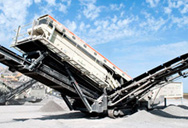
Development of specific grinding energy model - ScienceDirect
Specific grinding energy consumption is very high for hard and brittle materials. One of the reasons is the very low depth of cut at which these materials are ground. At low depth of cut specific grinding energy consumption …
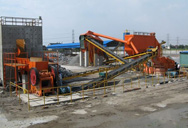
(PDF) The Integrated Energy Consumption Index for Energy ...
A testing methodology was developed to improve the parameters of multi-disc grinding, including the reduction of energy consumption, power input, product quality improvement, …
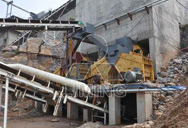
Breaking down energy consumption in industrial grinding mills
Grinding mills are infamous for their extremely low energy efficiency. It is generally accepted that the energy required to produce new mineral surfaces is les s than 1% of the electricity consumed...
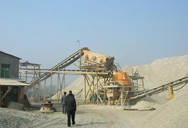
Raw Material Drying-Grinding - Cement Plant Optimization
Total power consumption for grinding circuit as a whole is also less by about 30% compared to closed circuit ball mill in spite of higher fan power. Feed size can be as large as 75 to 100 mm. …
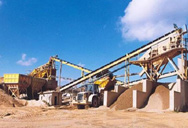
How much power does normal grinder consume? - Quora
Feb 16, 2020 · Normal Conventional wet grinder would generate 150 watts of power under normal weight and circumstances. Most wet grinders avail in the market have this as standard and run …

Chapter 7 Energy Use in the Copper Industry
mentation versus increased crushing or grinding energy also can minimize energy use and lead to savings.9 7Assuming diesel fuel cost of 30 centsper Iiter and electricity at 5 cents per kWh. …
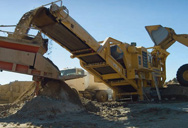
Ball Mill Design/Power Calculation
The power consumption per short ton will only be correct for the specified size reduction when grinding wet in closed circuit. If the method of grinding is changed, power consumption …
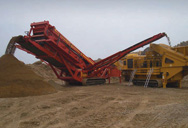
Breaking down energy consumption in industrial grinding mills
Results showed that on average, 79% of the supplied electrical energy was converted to heat absorbed by the slurry, 8% was lost through the drive system, and approximately 2% was …
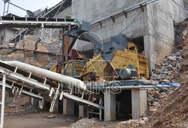
THE GRINDING EFFICIENCY OF THE CURRENTLY LARGEST …
Batch grinding tests were carried out on samples of the new feed to the regrind circuit. A conventional tubular ball mill was used for these batch tests. The tests followed the same procedures used by liming to estimate Vertimill specific energy consumption. The procedure involves grinding …
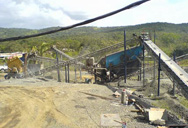
Energy consumption of two-stage fine grinding of Douglas ...
Grinding energy consumption is a function of the parti cle size of feed and product afected by material characteris tics, including stone species and moisture content, grinding systems, and …
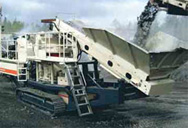
The Effects of Blasting on Crushing and Grinding ...
Energy Consumption in Crushing and Grinding The energy input to size ore fragments is large. Overall reduction, performed in a series of stages may be from an eighty percent feed size …