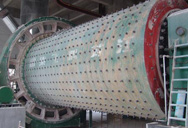
Understanding Reactions in Iron Ore Pellets - AusIMM
The interaction of these reactions produces a range of atmospheres across the diameter of the pellet that vary from oxidising at the pellet shell to reducing at the pellet core.
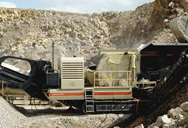
Chemical Reactions In Pelletizing Of Iron Ore
Chemical reactions in blast furnace during the iron ore , an iron ore blast furnace is a typical example of a shaft furnace extraction of iron in a blast furnace extraction of iron in a blast furnace the significant reactions occuring within the blast furnace can be described via the following steps showing how the reducing.Read more.
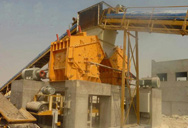
Understanding reactions in iron ore pellets
However, this oversimplifi es the different reaction paths of magnetite and carbon in iron ore pellets. At firing temperatures, gas diffusion controlled reactions such as …
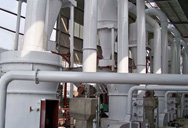
Introduction to Iron ore Pellets and Pelletizing processes ...
Iron ore pellet is a kind of agglomerated fines which has better tumbling index when compared with the iron ore and it can be used as a substitute for the iron ore lumps both in the BF and for DRI production. Pellets have good reducibility since they have high porosity (25 % to 30 %). Normally pellets are reduced considerably faster than sinter ...

Iron Ore Pelletizing - Fives in Combustion
Worldwide, the iron ore pelletizing industry has experienced major growth over the past five years for several reasons. They include continued demand for iron pellets in China and India to satisfy ongoing growth of their steel industries.
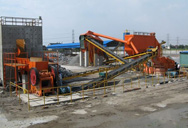
Iron Ore Pelletizing Process: An Overview | IntechOpen
Bentonite, an inorganic binder, has been the main binder used in the iron ore pelletizing process since the beginning of pellet production in the 1950s. Bentonite promotes the formation of ceramic bridges between particles, which can minimize the number of pellets that collapse during firing.

MODELING THE IRON ORE PELLETS REDUCTION ON SHAFT …
The process for pelletizing iron ore fines is an important operation unit for producing high quality of raw materials for the subsequent reduction processes such as blast furnace or direct reduction.
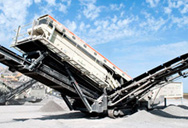
iron ore properties in blast furnace - iccastelgoffredo.it
iron ore properties in blast furnace; Use of Iron Ore Pellets in Blast Furnace Burden IspatGuru. Jun 13, 2014· Use of Iron Ore Pellets in Blast Furnace Burden Pelletizing is a process that involves mixing very finely ground particles of iron ore fines of size less than 200 mesh with additives like bentonite and then shaping them into oval/spherical lumps of 8-20 mm in …
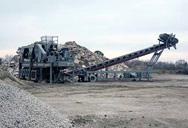
Recrystallization of Fe O During the Induration of Iron ...
Recrystallization of Fe 2 O 3 During the Induration of Iron Ore Oxidation Pellets 331 the dry balls were put into a corundum crucible and pushed into the preheating zone of the furnace step by step, preheated at the given temperature for a given period. Then the preheated pellets were taken out of the furnace and cooled in the air, or directly pushed

Study of the induration phenomena in single pellet to ...
The process for pelletizing iron ore fines is an important operation unit for producing high quality of raw materials for the subsequent reduction processes such as blast furnace or direct reduction. The process essentially involves production of green pellets and induration on a traveling grate furnace to promote inner partial melt and agglomeration that confers adequate …
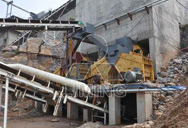
Direct Reduction Process - an overview | ScienceDirect Topics
Coal, dolomite and iron ore or pellets are fed into one end of a rotary kiln, while sponge iron and char are withdrawn from the other end. Primary and secondary airs are supplied to the kiln to initiate combustion and reaction processes ( Choudhury, 2014 ).
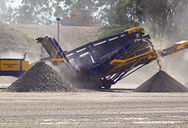
Pellets for Blast Furnace and Steel Production - YouTube
Jul 06, 2019 · Pellets are small balls of iron ore used in the production of steel. ... Pellets for Blast Furnace and Steel Production ... 10.3.2 Describe the essential reactions in the extraction of iron …
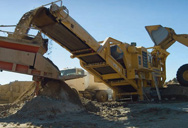
How Big Can Cleveland-Cliffs Be In The Iron Ore And Pellet ...
Mar 11, 2020 · Vale currently leads the iron ore and pellet market with about $29.3 billion in iron ore and pellet revenues over 2019, followed by Rio Tinto, BHP Billiton, and …
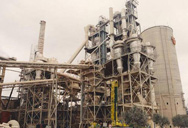
Blast furnace - Wikipedia
Coke, limestone flux, and iron ore (iron oxide) are charged into the top of the furnace in a precise filling order which helps control gas flow and the stone reactions inside the furnace. Four "uptakes" allow the hot, dirty gas high in carbon monoxide content to exit the furnace throat, while "bleeder valves" protect the top of the furnace ...
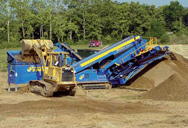
HOW A BLAST FURNACE WORKS - Foundry Gate
The iron ore, pellets and sinter are reduced which simply means the oxygen in the iron oxides is removed by a series of stone reactions. These reactions occur as
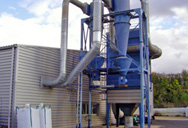
Iron Ore Pellets Induration Solutions - Metal 7
Iron ore green balls are soft and easy to break. So after the pelletizing and screening operations, iron ore pellets have to be hardened in a furnace through a firing process. Once fired, they can be handled, loaded in ships or trains and delivered to the end users.
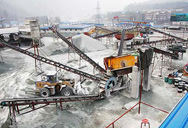
Direct reduced iron - Wikipedia
Direct-reduced iron has about the same iron content as pig iron, typically 90–94% total iron (depending on the quality of the raw ore) so it is an excellent feedstock for the electric furnaces used by mini mills, allowing them to use lower grades of scrap for the rest of the charge or to produce higher grades of steel.

DRI production | International Iron Metallics Association
Direct reduction of iron is the removal of oxygen from iron ore or other iron bearing materials in the solid state, i.e. without melting, as in the blast furnace. The reducing agents are carbon monoxide and hydrogen, coming from reformed natural gas, syngas or coal. Iron ore is used mostly in pellet and/or lumpy form.
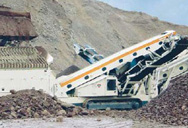
Cost Effectiveness Analysis of HYL and Midrex DRI ...
Midrex is a process by which iron ore pellets, lump iron ore or a combination of both is reduced in a vertical shaft/reduction furnace. The reduced material then flows through catalyst tubes where it is chemically converted into a gas containing hydrogen and carbon monoxide. As the iron ore moves down the furnace