
Ball Milling - an overview | ScienceDirect Topics
It is a solid-state mixing of powders, usually performed with ball mills, which enables intimate mixing of the constituents through repetitive stone deformation. By applying discontinuously high strain rates, ball milling enables the reduction of particle size in addition to the effective mutual dispersion of the processed phases.

Variables in Ball Mill Operation | Paul O. Abbe®
Ball mill operation is often regarded as something of a mystery for several reasons. Ball milling is not an art - it’s just physics. The first problem will ball mills is that we cannot see what is occurring in the mill. The other problem is that many of the independent variables are non-linear or have paradoxical effects on the end results.
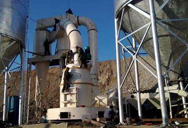
Ball mill - Wikipedia
It works on the principle of impact and attrition: size reduction is done by impact as the balls drop from near the top of the shell. A ball mill consists of a hollow cylindrical shell rotating about its axis. The axis of the shell may be either horizontal or at a small angle to the horizontal. It is partially filled with balls.

Ball Milling | Material Milling, Jet Milling | AVEKA
Ball milling is a size reduction technique that uses media in a rotating cylindrical chamber to mill materials to a fine powder. As the chamber rotates, the media is lifted up on the rising side and then cascades down from near the top of the chamber.
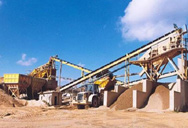
Ball Mill Loading - Dry Milling - Paul O. Abbe
Ball Mill Loading - Dry Milling. Ball Mill Loading (dry milling) When charging a ball mill, ceramic lined mill, pebble mill, jar mill or laboratory jar use on a jar rolling mill it is important to have the correct amount of media and correct amount of product.

Lab Report 1 and 2: PRACTICAL 1 : BALL MILLING
Dec 28, 2013 · Ball Mill is the equipment to be used for size reduction. It is a kind of grinder used for intermediate or fine grinding. Ball mill is a metal cylinder which rotates about its horizontal axis. The coarse sugar charged along with the metal balls breaks to fine powder by impact of …

Practical 1 : Ball Milling | TF Lab 1
Dec 23, 2013 · In ball mill, size reduction is done by both impact and attrition of particles. Rod mill is similar to ball mills but it uses long rods for grinding media. Autogenous mill is a self-grinding mill which is used in breakage of larger rocks.

Synthesis of Nanomaterials by High Energy Ball Milling
In particular, mechanical attributed contamination by the milling tools (Fe or WC) as well as ambient gas (trace impurities such as O 2, N 2 in rare gases) can be problems for high-energy ball milling. However, using optimized milling speed and …

Grinding Media & Grinding Balls | Union Process, Inc.
As the developer and manufacturer of industry-leading particle size reduction equipment, including Attritors (internally agitated ball mills) and DMQX horizontal media mills, Union Process is uniquely positioned to help you identify and source the correct grinding media for your application. Union Process customers know they can rely on our ...

Ball Mill - RETSCH - powerful grinding and homogenization
Ball mills are among the most variable and effective tools when it comes to size reduction of hard, brittle or fibrous materials. The variety of grinding modes, usable volumes and available grinding tool materials make ball mills the perfect match for a vast range of applications.
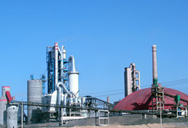
Ball Mill: Operating principles, components, Uses ...
A ball mill also known as pebble mill or tumbling mill is a milling machine that consists of a hallow cylinder containing balls; mounted on a metallic frame such that it can be rotated along its longitudinal axis. The balls which could be of different diameter occupy 30 -50% of the mill volume and its size depends on the feed and mill size.

Effect of Ball-Milling on the Oxygen Reduction Reaction ...
Here, we study the effect of ball-milling conditions and compositions of catalyst precursors comprising a silicon carbide-derived carbon (CDC) on the properties of the final catalysts, most importantly their activity toward the oxygen reduction reaction (ORR).

Factors Affecting Ball Mill Grinding Efficiency
The following are factors that have been investigated and applied in conventional ball milling in order to maximize grinding efficiency: a) Mill Geometry and Speed – Bond (1954) observed grinding efficiency to be a function of ball mill diameter, and established empirical relationships for recommended media size and mill speed that take this factor into account. As well, mills …
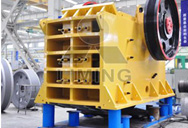
Milling Services: Jet, Ball & Attrition Milling | Steward ...
Our particle size reduction and sizing methods are used in a number of industries. We’re experts in attrition milling and ball milling, and have experience in mechanical alloying for ODS (oxide dispersion strengthened) applications. We also have PLC-controlled attrition mills that are equipped with data logging.
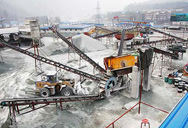
Effect of ball and feed particle size distribution on the ...
In this article, alternative forms of optimizing the milling efficiency of a laboratory scale ball mill by varying the grinding media size distribution and the feed material particle size distribution were investigated. Silica ore was used as the test material.
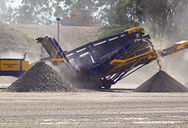
Mill (grinding) - Wikipedia
Ball mill. A typical type of fine grinder is the ball mill.A slightly inclined or horizontal rotating cylinder is partially filled with balls, usually stone or metal, which grind material to the necessary fineness by friction and impact with the tumbling balls. Ball mills normally operate with an approximate ball charge of 30%.

FM 306: SIZE REDUCTION AND SIEVING - IIT Bombay
Ball Mill: The equipment to be used for size reduction is ball mill. The ball mill is kind of grinder used for intermediate or fine grinding. Ball mill is a metal cylinder which rotates about its horizontal axis. The coarse material charged along with the metal …

Ball Mills - Mineral Processing & Metallurgy
Cylindrical Ball Mills. The only cylindrical ball mills in common use are those of the grate discharge type, the most important being the Marcy and the Allis-Chalmers mills. Fig. 10 illustrates the construction of the Marcy Ball Mill. The cylindrical shell and the feed and discharge heads are made of cast semi-steel.

Best way to determine the ball-to-powder ratio in ball ...
The tribochemical effects of MoSiMosiwder in the ball milling process have been studied by X-ray diffraction (XRD) and QM-4H milling machine. It has been found that the intensity of diffraction...

3 Benefits of Ball Mills | 3 Benefits Of
Jun 19, 2014 · The wet grinding with a ball mill includes a certain amount of water, or similar liquid, in order to increase the flow-ability of the materials that needs to be crushed. In the dry grinding process on the other hand, the capacity is affected by the reduced flow-ability of the material. Therefore, the flow-ability needs to be increased.